stratamania
Mythical Status
- Messages
- 12,137
I then need to enlist the help of the neck and the tremolo unit so I can ensure the pickguard is correctly lined up and in position. I use masking tape to keep it where it needs to be.
I then drill the pilot holes of 1.5mm with the pickguard in place. I remove the pickguard and then use a 2mm bit to widen the holes to a depth of about 3mm and countersink them to avoid finish pops.
BF (5) by stratamania, on Flickr
The pickguard is flush all the way around with the neck pocket.
BF (6) by stratamania, on Flickr
And a couple of tools that were used today that wanted to make an appearance.
BF (7) by stratamania, on Flickr
By the way do not rely on my measurements for pilot holes etc verify what you need to do for your own situation. Though of course these may be a reasonable starting point.
Next up will be fret levelling, crowning etc...
As always thanks for looking and feel free to ask relevant questions, leave a comment etc
I then drill the pilot holes of 1.5mm with the pickguard in place. I remove the pickguard and then use a 2mm bit to widen the holes to a depth of about 3mm and countersink them to avoid finish pops.
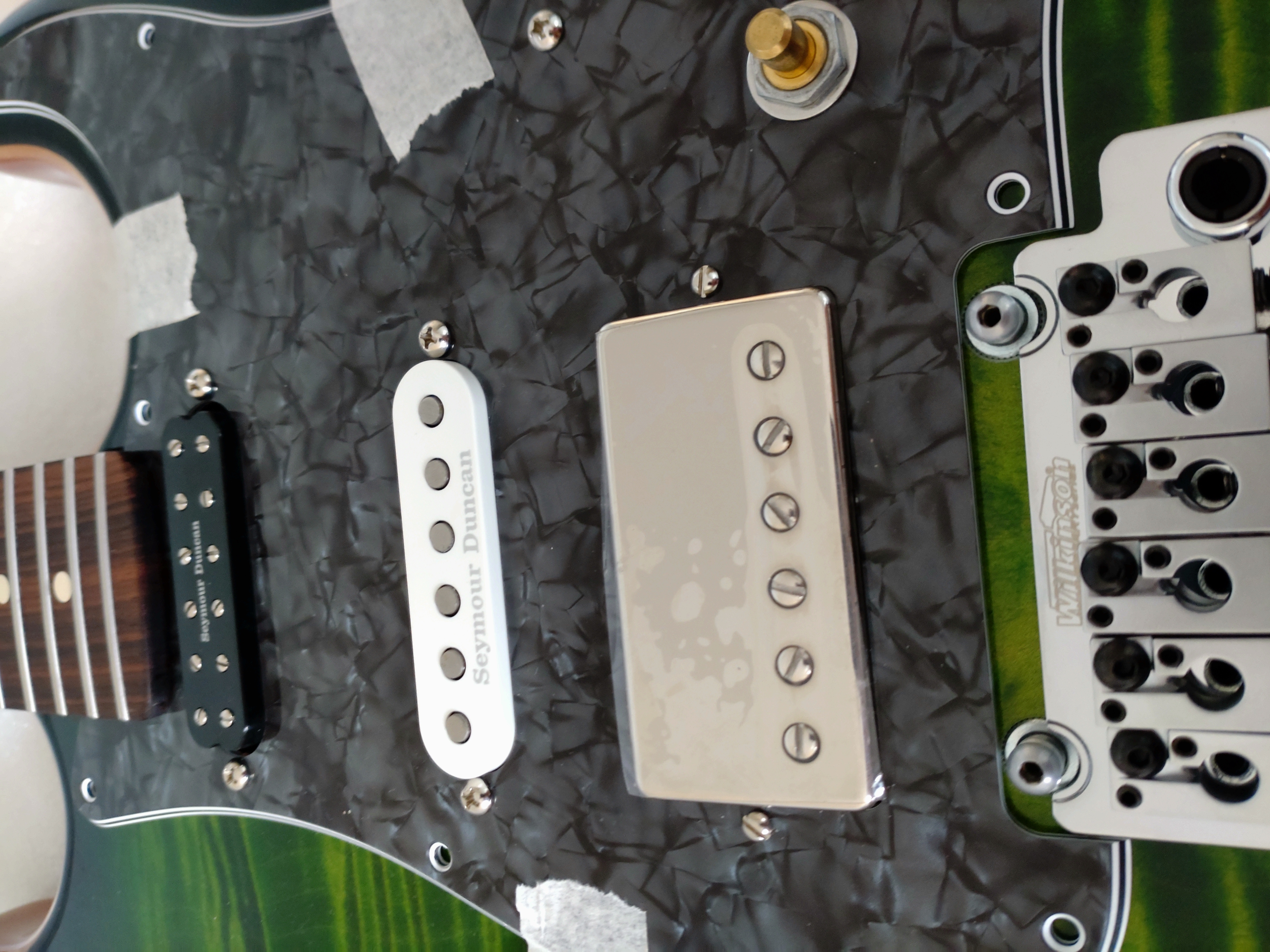
The pickguard is flush all the way around with the neck pocket.
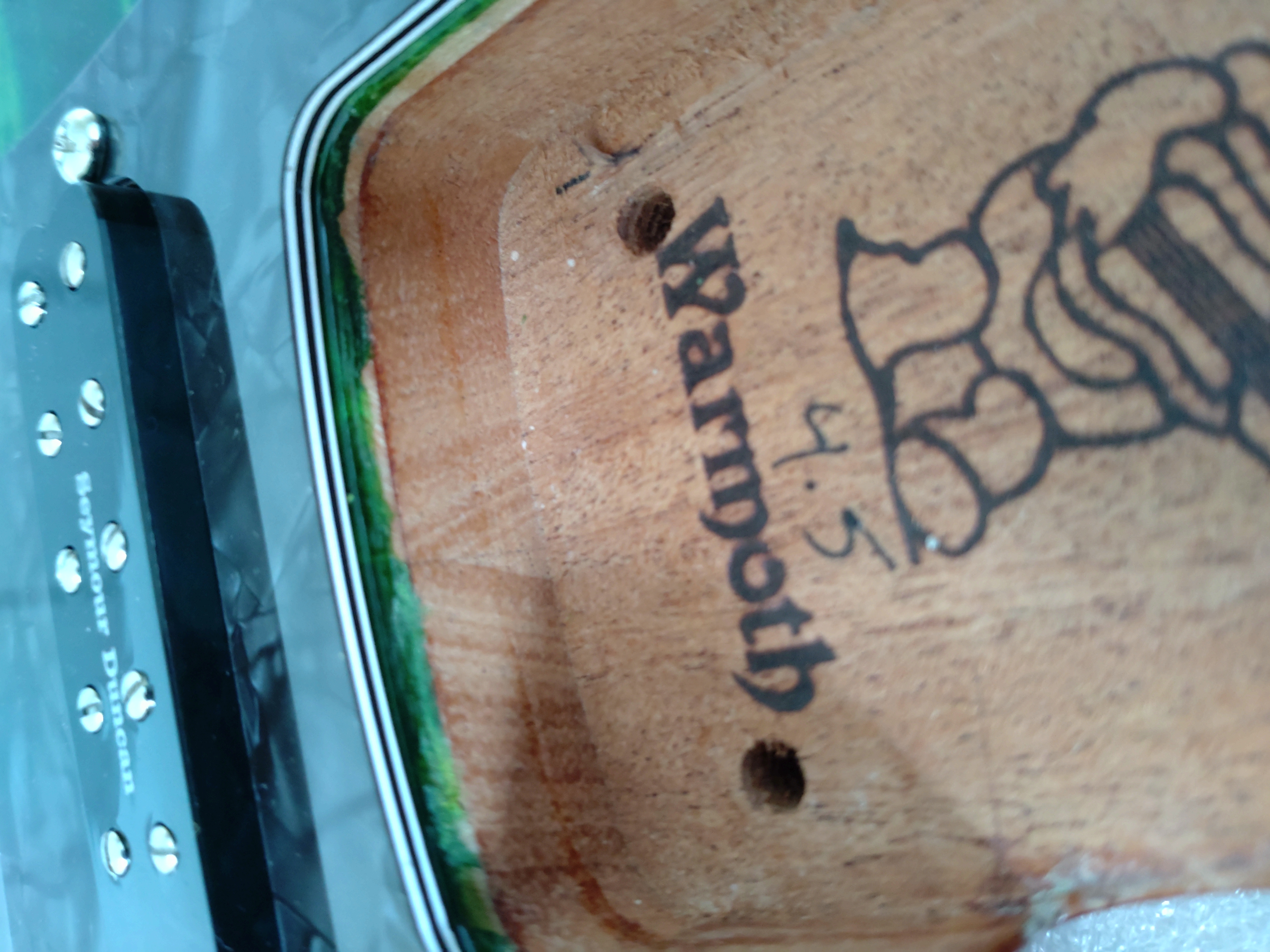
And a couple of tools that were used today that wanted to make an appearance.
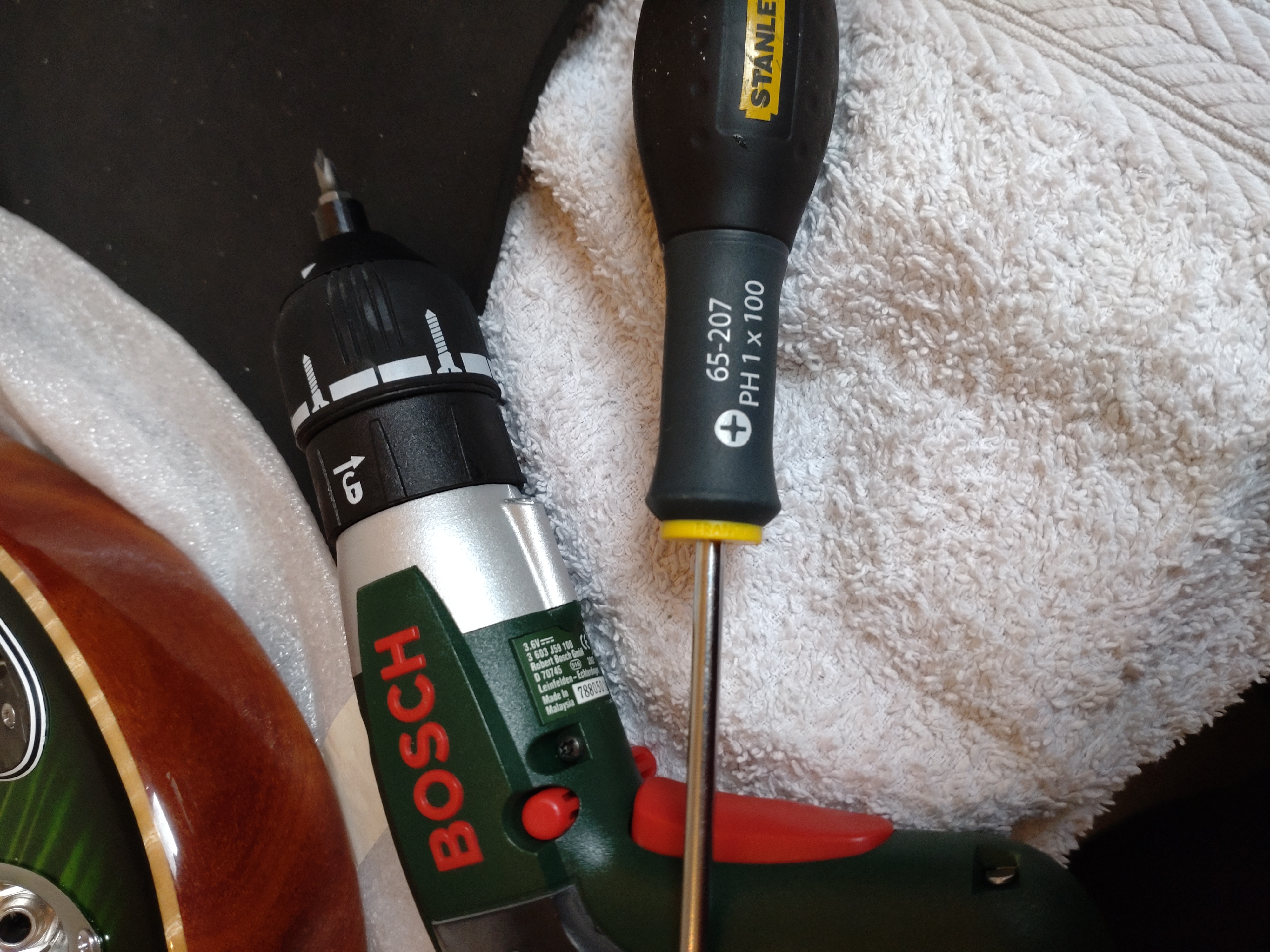
By the way do not rely on my measurements for pilot holes etc verify what you need to do for your own situation. Though of course these may be a reasonable starting point.
Next up will be fret levelling, crowning etc...
As always thanks for looking and feel free to ask relevant questions, leave a comment etc