fuzznut
Junior Member
- Messages
- 117
BigSteve22 said:I'll be interested to see how your re-profile goes. I put a Clapton Soft-Vee on my Jazzmaster and I'm still not sure about keeping it that way. It's been a little painful on my thumb playing barred chords.
I was thinking of either taking off some of the peak, or just getting a new Standard Thin profile. Taking the Vee down would certainly be less expensive, and since it's finished in satin lacquer, it wouldn't be all that hard to refinish.
Pictures as they become available, please.
I just finished the reprofiling. Yikes that was a lot of wood removed! :tard: I should've bought the 59 instead of the fatback and saved myself 2 hours of sanding. The 59 is a lot closer to what I want. You can remove the peak of the vee on the Clapton easily, although I believe it will still be thicker than the standard thin.
First thing I did was establish the front to back thickness with 100 grit on a random orbital sander. Sand, measure, sand , measure until the target thickness was met.
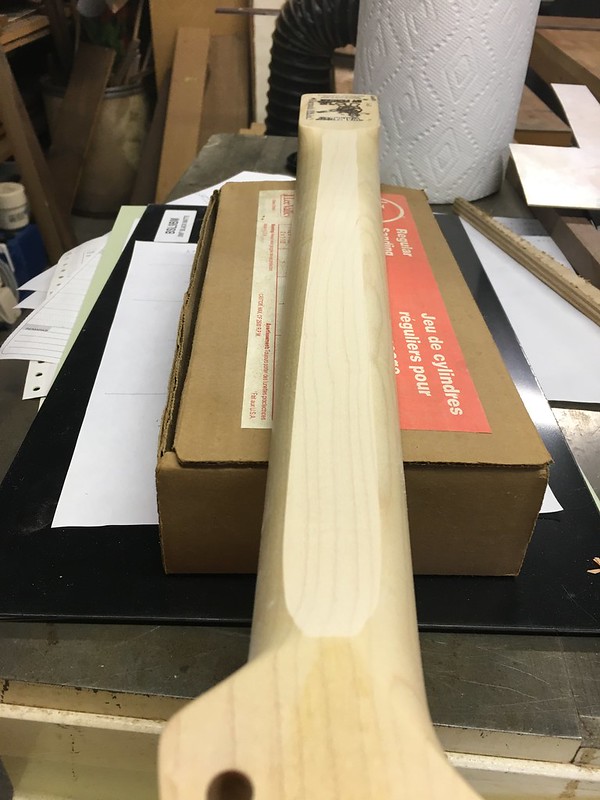
Then I started rough profiling with the ROS. After that it was all hand sanding with a block while checking the profile a million times with the gauges. After that, free hand sanding going progressively up with the grits. Not hard, but tedious.
[url=https://flic.kr/p/QFnvjL]
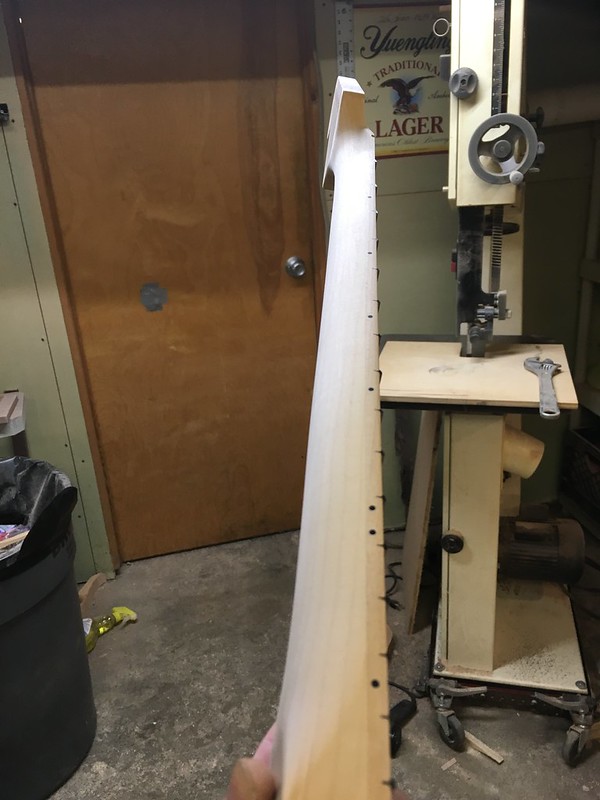
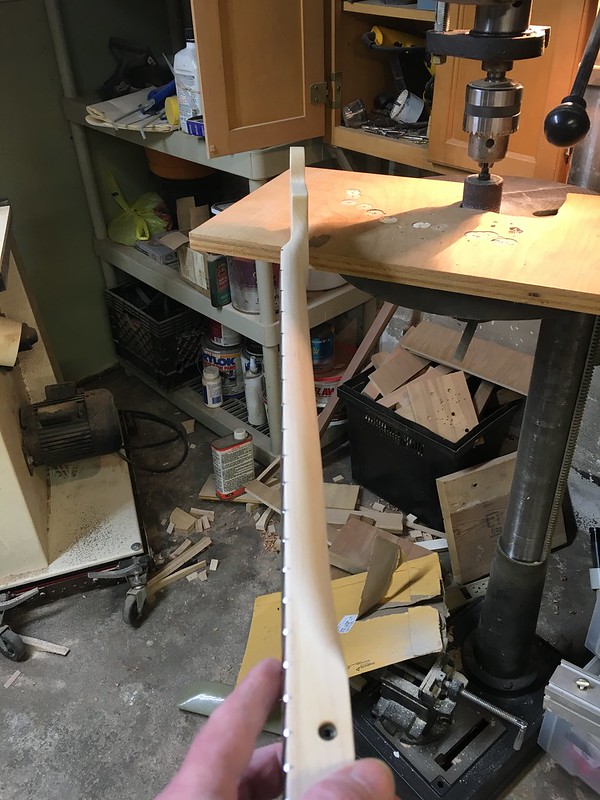