Cagey
Mythical Status
- Messages
- 24,425
One of our own here, BRK303, (we'll just call him Daniel since it's pronounceable) asked me to put together a Telecaster for him, and maybe document it a bit for fun. Basically, it's as the title describes - a bound satin black Telecaster with a highly figured roasted Maple neck. It's going to have somewhat subdued hardware, along with a few custom mods to the electricals that will make this a pretty unique instrument while still keeping fairly close the Telecaster design. The combination of the satin finish and subdued hardware should give it a sort of "NOS" (New Old Stock) look, as if it had been built long ago, but never used.
Where to begin? Hmm... Well, let's see what we're starting with...
It's a roasted Swamp Ash body with a Strat neck pocket, black satin finish, and pearloid binding. The roasted Swamp Ash is meant to provide that wood's characteristic tone as well as lightening it up a bit, but it's still 4.5 lbs (2.06kg). Comfort cuts all around - forearm, belly and neck heel. Standard Tele bridge/neck pickup routes and bridge drill pattern. Additionally, a pickup selector switch option was cut in the upper bout, but that's not what it's for. We'll get to that later. An attractive piece. The white pearloid binding against the black is a really nice accent.
Then, a body without a neck doesn't give you much to bite on, so...
Where do they grow this stuff? Geez, that's pretty! One of the best examples of figured roasted Maple I've seen. And that's with ME taking pictures. Imagine what it looks like in real life! The grain shimmers and moves under the light like a cat's eye gem.
I know I had "as delivered" fretboard pics as well, but I'll be damned if I can find them. Anyway, rest assured, it's every bit as lovely as the neck meat. We'll see more of it later, when we talk about fretting and whatnot.
The bridge is from Glendale Guitars and is a little different...
...in that it's been cut down a bit from the traditional Tele design while still keeping enough of the sides to give it The Look, and it's made of unplated cold-rolled steel. I'm not sure how they do it - I suspect it's tumbled - but there are none of the rough edges you might expect with such a raw-looking piece, with no evidence of it having been sanded/buffed/polished/ground or anything like that. It didn't come with saddles - those came separately from...somewhere (I can't remember or find a packing slip). I think they're Gotohs. Anyway, compensated brass barrels like these...
Of course, those are much too pretty as they sit, so we're gonna have to gracefully age them. We'll get to that later.
Knobs appear to be standard Tele knurled dome-tops, but they're made of cold-rolled steel as well for that "I found 'em in my long-departed great-uncle's workshop" look...
Most knobs like that are made of brass, then gold/chrome plated or painted black. Difficult to age gracefully with any kind of authenticity.
I don't have any shots of the control plate unassembled, but you'll see it later. It's the same deal as the bridge and knobs - cold-rolled steel.
Pickups are a set of Rumplestiltskin "Black Knight" units.
Never heard of 'em, so we'll find out later if they're worth the copper they're wound with. Nice box, though.
Tuners are a nice set of Schaller M6 mini-lockers, which I'm sure most of you are familiar with...
I use these quite a bit - they're high-quality parts. It hasn't been discussed yet, but I think a set of pearloid buttons would be nice on those. Match the binding, for one, and get away from the polished chrome that doesn't exist anywhere else on the instrument.
I'm sure I'm leaving some stuff out, but that should cover the major parts. Strap hangers, pots, switches, wire, etc. are all pretty much standard stuff. Although, just for documentation's sake, I should mention the switch going into the upper bout. One of these days, I'm gonna want another one and I don't want to have to search for hours like I did to find this one...
I got them at Digikey, PN 360-1829-ND. I know it doesn't look like much, but what's cool about it is that it's a full-size operator on a DPDT (on/on) mini switch. So, it'll fit into a standard Switchcraft location and look right, but it gives you a size and operation you can't get from Switchcraft.
Also, Danny found a nifty bezel for it...
Kind like a coin, in that it's stamped rather than silkscreened or engraved. Nice little part.
The switch and bezel combined present much more nicely than the typical "accessory" or "option" mini switch buried down in the control cluster...
Stay tuned, there's more to come!
Where to begin? Hmm... Well, let's see what we're starting with...


It's a roasted Swamp Ash body with a Strat neck pocket, black satin finish, and pearloid binding. The roasted Swamp Ash is meant to provide that wood's characteristic tone as well as lightening it up a bit, but it's still 4.5 lbs (2.06kg). Comfort cuts all around - forearm, belly and neck heel. Standard Tele bridge/neck pickup routes and bridge drill pattern. Additionally, a pickup selector switch option was cut in the upper bout, but that's not what it's for. We'll get to that later. An attractive piece. The white pearloid binding against the black is a really nice accent.
Then, a body without a neck doesn't give you much to bite on, so...


Where do they grow this stuff? Geez, that's pretty! One of the best examples of figured roasted Maple I've seen. And that's with ME taking pictures. Imagine what it looks like in real life! The grain shimmers and moves under the light like a cat's eye gem.
I know I had "as delivered" fretboard pics as well, but I'll be damned if I can find them. Anyway, rest assured, it's every bit as lovely as the neck meat. We'll see more of it later, when we talk about fretting and whatnot.
The bridge is from Glendale Guitars and is a little different...

...in that it's been cut down a bit from the traditional Tele design while still keeping enough of the sides to give it The Look, and it's made of unplated cold-rolled steel. I'm not sure how they do it - I suspect it's tumbled - but there are none of the rough edges you might expect with such a raw-looking piece, with no evidence of it having been sanded/buffed/polished/ground or anything like that. It didn't come with saddles - those came separately from...somewhere (I can't remember or find a packing slip). I think they're Gotohs. Anyway, compensated brass barrels like these...
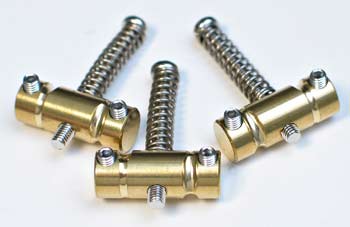
Of course, those are much too pretty as they sit, so we're gonna have to gracefully age them. We'll get to that later.
Knobs appear to be standard Tele knurled dome-tops, but they're made of cold-rolled steel as well for that "I found 'em in my long-departed great-uncle's workshop" look...

Most knobs like that are made of brass, then gold/chrome plated or painted black. Difficult to age gracefully with any kind of authenticity.
I don't have any shots of the control plate unassembled, but you'll see it later. It's the same deal as the bridge and knobs - cold-rolled steel.
Pickups are a set of Rumplestiltskin "Black Knight" units.

Never heard of 'em, so we'll find out later if they're worth the copper they're wound with. Nice box, though.
Tuners are a nice set of Schaller M6 mini-lockers, which I'm sure most of you are familiar with...

I use these quite a bit - they're high-quality parts. It hasn't been discussed yet, but I think a set of pearloid buttons would be nice on those. Match the binding, for one, and get away from the polished chrome that doesn't exist anywhere else on the instrument.
I'm sure I'm leaving some stuff out, but that should cover the major parts. Strap hangers, pots, switches, wire, etc. are all pretty much standard stuff. Although, just for documentation's sake, I should mention the switch going into the upper bout. One of these days, I'm gonna want another one and I don't want to have to search for hours like I did to find this one...


I got them at Digikey, PN 360-1829-ND. I know it doesn't look like much, but what's cool about it is that it's a full-size operator on a DPDT (on/on) mini switch. So, it'll fit into a standard Switchcraft location and look right, but it gives you a size and operation you can't get from Switchcraft.
Also, Danny found a nifty bezel for it...

Kind like a coin, in that it's stamped rather than silkscreened or engraved. Nice little part.
The switch and bezel combined present much more nicely than the typical "accessory" or "option" mini switch buried down in the control cluster...

Stay tuned, there's more to come!