aguyinaustintx
Junior Member
- Messages
- 88
I am contemplating a build that uses a roasted mahogany body. My thinking is that roasting mahogany will darken the color and reduce its weight, so I decided to try it in a conventional kitchen oven.
The first test was conducted by breaking off part of a scrap mahogany headplate veneer board, approx. 1/8" thick. The piece was placed in the oven before it was turned on. The temperature was slowly brought up to 360 degrees F over the course of 1 1/2 hours. It was roasted at 360 for one hour. The kitchen had a bit of a fireplace smell, or as if something unfamiliar was being baked. The oven was then turned off, and the piece was taken out after it reached room temperature. The piece was glued back on to the unroasted board. The board was crudely finished in a few layers of shellac to approximate the finished color. The piece appears to the left in the photograph below.
The next test was run on a piece of mahogany approximately 1" thick. The baking schedule was similar to the previous test, except that the 360 degree phase lasted for 1 1/2 hours instead of 1. The toasted piece was cut into two, and one piece was finished in shellac. The results appear below. An unroasted piece is included, with one half of it finished in shellac. Prior to roasting, the piece measured at 8.6% moisture using a pin-style moisture meter. After roasting, the moisture level was too low to register on the meter.
I like the resulting look. My next step will be to roast a mahogany electric guitar blank.
The first test was conducted by breaking off part of a scrap mahogany headplate veneer board, approx. 1/8" thick. The piece was placed in the oven before it was turned on. The temperature was slowly brought up to 360 degrees F over the course of 1 1/2 hours. It was roasted at 360 for one hour. The kitchen had a bit of a fireplace smell, or as if something unfamiliar was being baked. The oven was then turned off, and the piece was taken out after it reached room temperature. The piece was glued back on to the unroasted board. The board was crudely finished in a few layers of shellac to approximate the finished color. The piece appears to the left in the photograph below.
The next test was run on a piece of mahogany approximately 1" thick. The baking schedule was similar to the previous test, except that the 360 degree phase lasted for 1 1/2 hours instead of 1. The toasted piece was cut into two, and one piece was finished in shellac. The results appear below. An unroasted piece is included, with one half of it finished in shellac. Prior to roasting, the piece measured at 8.6% moisture using a pin-style moisture meter. After roasting, the moisture level was too low to register on the meter.
I like the resulting look. My next step will be to roast a mahogany electric guitar blank.
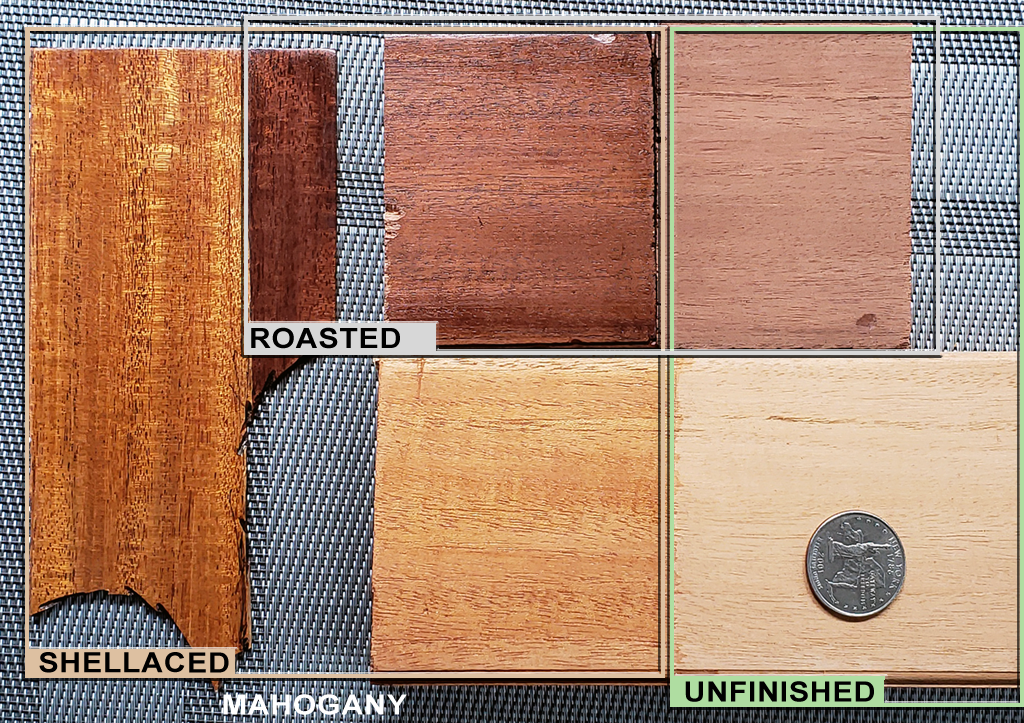